Successful demonstration of VAM processing
The only VAM technology that has so far proven to be commercially feasible on a large-scale basis is a system at the West Cliff Colliery of BHP Billiton, Australia (Somers and Schultz, 2008). The installation is called WestVAMP (West Cliff Colliery Ventilation Air Methane Plant) and is based on theVOCSIDIZERtechnology developed, patented and supplied by MEGTEC Systems.
Using VAM at a concentration of 0.9 per cent, high-grade steam is generated and used to drive a conventionalpower plantsteam turbine. The plant is thereby using a fuel consisting of ventilation air with more than 99 per cent air. It is processing 20 per cent of the ventilation air from the mine shaft, while driving a conventional 6MW(e) steam turbine and reducing emissions by an estimated 250,000 tonnes CO2-eq per year.
Operated during a few months in 1994, at the Thoresby Mine in the UK, MEGTEC first demonstrated that their VOCSIDIZER technology could efficiently abate VAM emissions. In principle, the VOCSIDIZER is a very well-insulated steel box with a bed consisting of a heat-exchange-efficient ceramic bed. Initially, the centre portion is heated to 1000°C. Then, the ventilation air containing CH4 in dilute form is passed through the bed. At the natural
-
- Figure 12.1 Cut-away illustration of the VOCSIDIZER
Source: MEGTEC
oxidizing temperature of CH4 the gas is oxidized, releasing energy that, by efficient heat exchange, is conserved and used to heat the next incoming portion of ventilation air up to VAM oxidizing temperature. In order to keep the hot oxidizing zone in the centre of the equipment, the direction of flow is alternated. A cut-away illustration is shown in Figure 12.1.
In 2001 to 2002, a second demonstration was made at the Appin Colliery of BHP in Australia (partly funded by ACARP, the Australian Coal Association Research Program). This trial demonstrated two important aspects, namely: (1) stability of operation - that the process could handle the natural swings in VAM concentration in a coal mine ventilation shaft (in order to demonstrate this, the installation was successfully operated for 12 months); and (2) energy recovery - the energy released in the VOCSIDIZER oxidation process was successfully utilized to generate steam.
The ultimate demonstration of the VOCSIDIZER technology was made in the WestVAMP project at the West Cliff Colliery of BHP Billiton in Australia. This VAM power plant was officially inaugurated on 14 September 2007 after several months of successful operation. The project was partly funded by the Australian Greenhouse Office and has two revenue streams - the value of the electricity generated and 'carbon credits' sold within the New South Wales trading scheme. The WestVAMP installation had, by 2009, generated over 80GWh of electricity and 500,000 carbon credits (tonnes CO2-eq) traded on the local New South Wales trading scheme. In the first fiscal year of operation, BHP Billiton reported plant availability to be at 96 per cent, including two
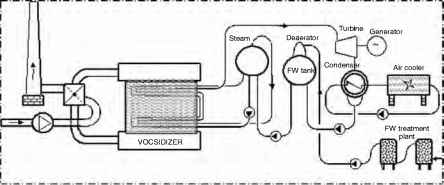
Figure 12.2 Principle process diagram of a VAM power plant based on the VOCSIDIZER
Source: MEGTEC
Figure 12.2 Principle process diagram of a VAM power plant based on the VOCSIDIZER
Source: MEGTEC
planned maintenance shutdowns (see Booth, 2008). The plant can be described as a conventional steam-based power plant, using the VOCSIDIZER as an unconventional furnace capable of operating on an extremely lean fuel. A principle process diagram of a VAM power plant based on the VOCSIDIZER technology is shown in Figure 12.2.
The VOCSIDIZER technology for VAM processing has also been demonstrated by CONSOL Energy in West Virginia - with support from the US EPA (United States Environmental Protection Agency) and the US Department of Energy - and by the ZHENGZHOU Mining Group in the Henan Province of the People's Republic of China. The Chinese installation is the first VAM processing plant of any kind in the world to be formally approved by the UNFCCC for the generation of carbon credits.
Technically, the VOCSIDIZER technology is essentially based on the very efficient heat exchange between the air being processed and the internal configuration of the system. The efficiency of the system means that a VAM concentration of only 0.2 per cent is required to maintain the oxidizing process. There is no combustion chamber - instead the oxidation takes place inside a special ceramic bed. There are also no 'hot spots' or periods of open flame combustion, meaning that significant production of nitrogen oxides (NOx) is avoided.
Continue reading here:Which options are available to reduce methane emissions and what are the costs of the options
是这篇文章helpful?