存在的技术
3.5.2.1气体和水蒸气重整光烃类蒸汽转化制氢的主要技术今天最大的单一训练工厂生产480 tH2 d 1。主要的能量来源是经常bet雷竞技 ,那么这个过程称为蒸汽甲烷重整鼻中隔黏膜下切除术后(),但也可以是其他碳氢化合物,如石脑油。这个过程始于从提要中硫化合物的去除,因为这些是毒药当前镍基催化剂,然后蒸汽添加。改革的反应(1),这是吸热的,发生在催化剂在高温下(800°C - 900°C)。热提供反应堆管通过燃烧燃料(二次燃料)的一部分。改革后的气体冷却的废热锅炉产生的蒸汽所需的反应和传递到公司系统的转变。转变反应堆在一个或两个阶段用于大多数公司的合成气转化为二氧化碳(放热反应3)。
传统的两级公司转换减少CO浓度合成气氢(或)降至0.2 - -0.3%。高温转变反应堆操作400°C和550°C之间使用一个iron-chromium催化剂离开出口气体有限公司2%和3%之间(干基)。可以使用铜基催化剂在温度从180°C - 350°C和离开从排气的0.2 - -1%股份。更低的公司内容倾向于更高的二氧化碳复苏。然后冷却天然气和氢气产生的CO2 / H2分离步骤。直到大约30年前,二氧化碳被使用化学(溶剂)吸收过程如胺或热碳酸钾和被拒绝大气作为一个纯粹的流从再生器的顶部。有很多这样的工厂仍在使用和二氧化碳捕获。
现代植物,然而,使用变压吸附器(PSA),在H2以外的气体吸附在一组交换床层含有固体吸附剂如活性炭、氧化铝和沸石(见PSA的完整描述3.5.2.9节)。H2退出PSA(通常约为2.2 MPa)可以有纯度高达99.999%,这取决于市场需求。二氧化碳是包含在一个流,从再生周期,其中包含一些甲烷和氢气。流是改革者,用作燃料燃烧空气和二氧化碳最终被改革者烟气排放到大气中。因此,鼻中隔黏膜下切除术后从现代捕获二氧化碳的植物需要的一个燃烧后上面描述的过程在3.3节。另外,PSA系统可以设计不仅高纯H2的复苏,而且恢复纯二氧化碳和燃气作为第三产品流。
在设计研究中对于大型现代植物(总容量720 tH2 d 1)的总体效率6.0 MPa H2天然气没有二氧化碳捕获的二氧化碳排放,估计为76%,低热值,排放9.1千克二氧化碳/公斤H2 (IEA温室气体,1996)。这个过程可以修改(成本)提供近纯二氧化碳副产品。一种可能性是去除大部分的二氧化碳从转移,冷却合成气在“湿”二氧化碳去除植物适当的胺溶剂。在这种情况下,CO2-deficient合成气退出胺洗涤器传递给一个PSA单元相对纯H2恢复和PSA净化气体燃烧额外的天然气提供所需的改革者热量。二氧化碳是通过加热和加压胺溶剂的回收运输。考虑到功率压缩二氧化碳(11.2 MPa)降低了约73%的效率和发射率1.4 kgCO2 / kgH2,而二氧化碳8.0 kgCO2 / kgH2去除率。2 2 2
3.5.2.2部分氧化部分氧化的气体和轻碳氢化合物(POX)过程(反应2),燃料与纯氧反应在高压力。这个过程是放热的,发生在高温下(通常是1250°C - 1400°C)。合成气反应所需的热量是由部分燃烧的燃料和不需要外部加热。同,合成气将冷却,和转移
二氧化碳从混合物中删除。评论的3.5.2.5气化煤、石油残渣,鼻中隔黏膜下切除术后或生物质分离二氧化碳从合成气上面同样适用于痘过程。今天痘是常用的一种技术,效率低于,但燃料,可以处理的范围更广泛。
提供大规模制氢,氧从低温空气分离装置(ASU)。高投资和能源消耗ASU的更高的效率和更低的成本补偿的气化过程和N2的缺失(空气中的)合成气,大大降低分离成本。然而对于预燃de-carbonization应用程序,将使用氢作为燃料的燃气轮机,它将需要稀释H2与N2或蒸汽减少燃气轮机燃烧室的火焰温度,不限制排放水平。在这种情况下,x最有效的系统将使用空气作为氧化剂和产生一个H2 / N2混合燃料(方式et al . 2005年)
3.5.2.3 Auto-thermal改革的气体和碳氢化合物
的自热式改革(ATR)过程可以被认为是上述两个过程的结合。鼻中隔黏膜下切除术后所需的热量在反应堆产生的部分氧化反应(2)使用空气或氧气,但由于蒸汽提供核反应堆以及过剩的天然气,吸热反应(1)改革发生在一个反应堆的催化部分下游痘的燃烧器。的蒸汽使高氢燃料转换成在一个较低的温度。自热过程的操作温度通常是950 - 1050°C,虽然这取决于流程的设计。过程的优势,相比,是核反应堆的降低投资成本和无排放的二氧化碳热释放内部,尽管这在很大程度上抵消了制氧机的投资和运营成本。燃料,可以处理的范围是鼻中隔黏膜下切除术后相似的过程,但是必须硫原料气自由。二氧化碳捕获完成如上所述蒸汽甲烷重整。
3.5.2.4天然气加热的改革者
每一代的三个合成气技术,ATR和痘产生高温气体必须冷却,生产在每种情况下的蒸汽流量超过所需的改革和转变的反应。可以减少这种生产过剩,例如,使用预热空气和鼻中隔黏膜下切除术后改革前的植物。另一种方法是使用热合成气,离开主反应堆,作为一个管状的壳程流体加热蒸汽/烃重整反应器可以串联操作,或并行,与主反应堆(Abbott et al ., 2002)。增加二次气体加热改革者将增加33%的氢和消除多余的蒸汽生产。提高总体效率和特定的资本成本通常是降低15%。再次,二氧化碳捕获像前面描述的那样完成蒸汽甲烷重整。
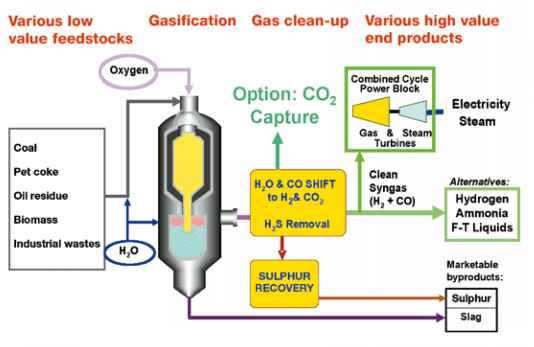
图3.14气化过程的简化示意图显示选项与二氧化碳捕获和电力、氢或化工生产。
气化(见图3.14)是一个化学过程,旨在制造高附加值产品(化工、电力、清洁合成燃料)等低价值的固体原料煤、炼油残留物,或生物量。气化是部分氧化反应(2),虽然蒸汽也提供给反应堆在大多数过程。固定床,可以使用流化床气化炉或携入的流。这可以有非常不同的特点对氧化剂(空气或氧气),操作温度(最高可达1350摄氏度),操作压力(0.1 7 MPa),给水系统(或干燥水泥浆)、合成气冷却方法(水淬或通过辐射和对流热交换器)和气体净化系统部署。这些替代设计选项确定原料的分数转换成合成气,合成气成分和成本。经济学强烈依赖规模、气化通常被认为是只适合大型植物。气化炉的输出包含公司,H2,二氧化碳水和杂质(如氮气、COS、硫化氢、HCN、NH3、挥发性微量元素和Hg),必须妥善管理。
全球商业气化项目的调查发现128操作气化厂366气化炉生产42700 MWt的合成气(NETL-DOE, 2002 Simbeck, 2001 A)。也有大约24500 MWt的合成气项目开发或建设,每年将增加4000 - 5000 MWt的合成气。原料主要是更高等级的煤炭和石油残留。大多数商业气化增长在过去的20年中涉及entrained-flow气化炉,因为有三个系统在市场上竞争。最近商业气化发展主要与工业氨生产、工业polygeneration(清洁合成气用于发电和蒸汽溢价合成气化学物质)和IGCC发电厂。商业经验与生物质气化和流化床气化是有限的。
二氧化碳捕获技术是建立了气化系统,使化学品和合成燃料(NETL-DOE, 2002)。各种气体NH3植物(许多中国人)包括纯H2和CO2分离速度高达3500 tCO2 d 1 /工厂。南非植物使费燃料和化学品和北达科他州植物合成天然气(合成天然气)煤也几乎纯净的二氧化碳产生大的溪流。图3.15显示了一幅的北达科他州气化厂3.3 MtCO2一年级使用冷藏methanol-based捕获,物理溶剂擦洗过程(Rectisol过程,参见3.5.2.11和表3.2)。大多数捕获二氧化碳排放和1.5 Mtonnes一年级的流目前管线式Weyburn,加拿大采油和二氧化碳存储项目(见第五章)。
当二氧化碳捕获是一个客观,O2-blown和高压系统是首选,因为更高的二氧化碳分压。De-carbonization通过气化需要低能量处罚二氧化碳捕获比燃烧后捕获时只考虑分离阶段,因为二氧化碳可以恢复部分压力上涨3个数量级。这大大减少了二氧化碳吸收器大小、溶剂循环率和二氧化碳汽提能量需求。然而,额外的能量转移公司的罚分合成气中二氧化碳和系统的其他部分(参见示例IGCC电站二氧化碳捕获在图3.6和3.7)。最近分析了沥青煤(见,例如,IEA温室气体2003)建议使用简单的高压
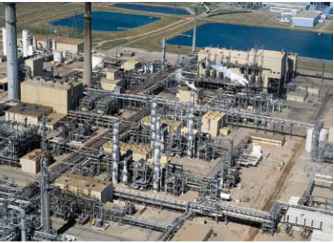
图3.15北达科他州煤气化厂3.3 MtCO2 yr1捕获使用冷甲醇,物理溶剂过程(集群4高列中间的图片代表了硫化氢和二氧化碳捕获流程;捕捉到流的一部分用于三次采油Weyburn二氧化碳存储,萨斯喀彻温省,加拿大)。
图3.15北达科他州煤气化厂3.3 MtCO2 yr1捕获使用冷甲醇,物理溶剂过程(集群4高列中间的图片代表了硫化氢和二氧化碳捕获流程;捕捉到流的一部分用于三次采油Weyburn二氧化碳存储,萨斯喀彻温省,加拿大)。
entrained-flow气化炉与水泥浆的饲料和直接水淬紧随其后的是“酸”(sulphur-tolerant)转变反应堆最后co-removal物理吸收的二氧化碳和硫化氢。与酸的变化,热生离开气化炉合成气只需要一个冷却周期和更少的处理。氧气需求增加美联储浆气化炉和更高的转换效率下降周期与淬火冷却效率损失。类似的趋势也指出,从沥青转向低秩次烟煤和褐煤(布列塔尼的事实,2002)。一些分析(如Stobbs和克拉克,2005年)表明,预燃室的优势在燃烧后de-carbonization可能小或消失煤级煤转换entrained-flow气化炉。高压,流化床气化炉可能更适合使用煤级煤,生物质和各种碳质废物。虽然有成功的例子示范的气化炉(如高温温克勒,Renzenbrink et al ., 1998),几乎没有商业规模的操作经验。
合成气中的H2S必须删除的IGCC电站的ppm水平符合二氧化硫排放法规和水平远低于1 ppm对植物化学物质或合成燃料,以保护合成催化剂。如果必须提供二氧化碳储存在相对纯粹的形式,常见的做法是先恢复硫化氢(这是比二氧化碳更容易吸收)从合成气(以及少量的二氧化碳)在一个回收装置,其次是减少硫化氢元素硫在老人植物和尾气净化,和随后的复苏大部分剩余的二氧化碳在一个单独的下游单位。另一个选择就是恢复硫磺硫酸的形式(McDaniel Hormick, 2002)。如果H2S / CO2 co-storage是允许的,但是,它常常是理想的恢复H2S和CO2在同一个物理吸收单元,这将导致温和系统节省成本(IEA温室气体,2003;拉尔森和任,2003;克鲁兹et al ., 2005)特别是在通常的可怜的销售前景副产品硫磺和硫酸。尽管co-storage H2S和CO2经常追求加拿大西部作为酸的酸性气体管理策略天然气项目(巴楚和甘特,2005),目前尚不清楚co-storage会经常在大尺度上可行的——一个典型的各种气体能源项目将涉及每年二氧化碳存储率1 - 4 Mtonnes一年级,而所有48个加拿大项目的总二氧化碳存储率目前只有0.48 Mtonnes一年级(巴楚和甘特,2005)。
3.5.2.6整体煤气化联合循环(IGCC)发电的煤IGCC、合成气退出粒子的气化炉是清洁,硫化氢和其他污染物,然后焚烧发电通过燃气轮机和蒸汽轮机联合循环。合成气生成和转换为电能在同一网站,避免高成本的管道运输与热值合成气(只有大约1/3的天然气)和成本效益利用机会让额外的电力使用蒸汽联合循环汽轮机的合成气冷却。IGCC发展主要驱动力最初是利用燃气轮机技术的持续发展的前景,易于实现低水平的空气污染物排放污染物时从合成气,并大大减少过程流卷从燃烧烟气流相比,在低压力和稀释从空气中氮。
自该技术最初是在1980年代,大约4 GWe IGCC电厂已建成。其中大部分由石油或petcoke推动能力;小于1 GWe总数的是专为煤(IEA CCC, 2005)和3 4植物目前操作对煤炭和/或petcoke。这样的经历已经证明IGCC load-following能力,尽管这项技术可能会主要用于基本负荷的应用程序。所有燃煤IGCC项目补贴,而只有意大利油基IGCC项目补贴。其他polygeneration项目在加拿大、荷兰和美国,以及油基IGCC在日本,没有补贴(Simbeck, 2001)。
IGCC尚未部署更广泛,因为激烈的竞争从天然气联合循环(NGCC)无论天然气是现成的低价,因为IGCC电站燃煤成本不低于煤粉解雇蒸汽发电植物和因为可用性(可靠性)的担忧。IGCC可用性改进了近年来商业规模示范单位(沃巴什河能源,2000;麦克丹尼尔和Hornick), 2002)。同时,可用性更好的为工业polygeneration和IGCC项目在炼油厂和化工厂人员经验丰富的化学过程。最近在美国天然气价格上涨也增加了IGCC的兴趣。
由于气化的优势二氧化碳捕获高部分压力上面所讨论的,IGCC可能对煤炭发电厂在碳排放受到限制的吸引力(Karg Hannemann, 2004)。二氧化碳捕获预燃系统是商业上准备好了,但是,没有IGCC植物将二氧化碳捕获尚未建立。利用现有技术,能源的平均估计罚款和燃料的使用增加二氧化碳去除的影响相对于其他捕获系统在图3.6和3.7和显示IGCC的未来的潜在选项。数字3.6和3.7中的数据还表明,一些IGCC选项(即可能不同于他人。,泥浆美联储和淬火冷却和干燥饲料和合成气冷却)和他们的相对优势的资本成本的植物和权力的交货成本在3.7节讨论。
从煤与二氧化碳捕获3.5.2.7氢
相对于集中研究煤IGCC技术与二氧化碳捕获,很少有研究在公共领域在H2来自煤经气化二氧化碳捕获(NRC, 2004;帕森斯2002 a, b;灰色和汤姆林森,2003;基et al ., 2005;克鲁兹et al ., 2005),尽管这H2商业技术逐渐完善,如上所述。与商业技术,H2和CO2捕获系统中可以通过煤气化生产类似于煤与二氧化碳捕获IGCC电站。符合上述设计建议煤炭IGCC电站(IEA温室气体,2003),下面是描述从设计研究煤炭H2体系,生产,使用最佳可用技术,1070年MWt H2的高硫(3.4%)烟煤(基et al ., 2005;克鲁兹et al ., 2005)。在基地的情况下设计、合成气生产在一个携入的流淬火气化炉操作7 MPa。合成气是冷却,清洗颗粒物,转移(主要是氢气和二氧化碳)酸水气体反应堆的转变。经过进一步冷却,硫化氢是使用一个物理溶剂从合成气中删除(Selexol)。二氧化碳从合成气中删除,再次使用Selexol。被剥夺后从溶剂、硫化氢转化为元素年代老人单位和工厂提供了消除残余硫排放的尾气净化;和二氧化碳排放或干燥和压缩到150 atm地下管道运输和存储。提取高纯度氢气在6 MPa的H2-rich合成气通过变压吸附(PSA)单位。PSA净化气体压缩和燃烧在传统的燃气轮机联合循环发电78兆瓦和39兆瓦的电力超过现场电力需求在没有和二氧化碳捕获情况下,分别。基本情况分析,H2制造的有效效率估计64%二氧化碳排放和61%二氧化碳捕获,而相应的发射率16.9 kgCO2和1.4 kgCO2 / kgH2,分别。捕获的情况下,二氧化碳去除率为14.8 kgCO2 / kgH2。各种替代系统配置进行了探讨。 It was found that there are no thermodynamic or cost advantages from increasing the electricity/H2 output ratio, so this ratio would tend to be determined by relative market demands for electricity and H2. One potentially significant option for reducing the cost of H2 with CO2 capture to about the same level as with CO2 vented involves H2S/CO2 co-capture in a single Selexol unit, as discussed above.
3.5.2.8碳基液体燃料和产品
正如在第二章所讨论的,清洁合成高H / C比燃料可以由合成气通过气化煤或其他低H / C比原料。潜在的产品包括合成天然气,费托柴油/汽油、二甲醚、甲醇和汽油与甲醇通过美孚的过程。副产品通常是一个相对纯净的二氧化碳流,可以捕获和存储。
煤炭衍生费托合成燃料和化学品生产以商业规模在南非;煤甲醇是在中国生产,在一个我们工厂;和煤炭生产合成天然气在北达科塔州(美国)植物(NETL-DOE, 2002)。自2000年以来,1.5 MtCO2北达科他州的一年级合成天然气工厂(参见图3.15)已经通过管道运输,300公里Weyburn油田在萨斯喀彻温省,加拿大采油与二氧化碳储存。
合成燃料生产涉及O2-blown气化合成气,气体冷却,气体净化,水煤气转移和酸性气体(H2S / CO2)删除。随后清洁合成气催化地转化成燃料合成反应器和不可交易的合成气分离液体燃料产品。此时也最不改变的气体回收合成反应器产生额外的液体燃料和剩下的不改变的天然气发电用于现场需求,或合成气通过合成反应器只传递一次,和所有不改变的合成气用于其他目的,例如,发电,出售给电网以及现场使用。后者一旦通过选项通常是更具竞争力作为技术选项(威廉姆斯,2000;灰色和汤姆林森,2001;拉尔森和任,2003;侯赛因等,2005)。
新的浆液合成反应堆让CO-rich曾经通过配置特别具有吸引力(例如,煤成)合成气通过高一旦通过转换成为可能。这一次通过系统、水煤气转移反应堆通常是将上游的合成反应器产生的H2 / CO比率最大化合成燃料转换合成反应器。需要把大部分二氧化碳从合成气转向合成燃料转换最大化。此外,由于硫化氢合成催化剂是非常敏感和各种微量污染物,这些必须被移除之前合成反应器非常低的水平。大多数微量金属可以删除在低成本使用活性炭过滤器。二氧化碳脱除合成气合成反应器的上游是一个低成本、部分de-carbonization选项,尤其是硫化氢和二氧化碳co-captured co-stored作为酸性气体管理策略(拉尔森和任,2003)。进一步de-carbonization可以通过系统,实现一次增量成本更高,通过添加附加转变反应堆下游合成反应器的二氧化碳中恢复,并使用CO2-depleted H2-rich合成气发电或混合电力+ H2 polygeneration的配置(见图3.16)。H2和电力生产的相对量主要取决于相对要求,似乎并不存在热力学或成本优势为特定H2 /发电量的比率(基et al ., 2005;克鲁兹et al ., 2005)。当合成气脱碳的上游和下游合成反应器(见图3.16)是可行的捕获和储存的二氧化碳高达90%的碳原原料除外
-
- 图3.16制造液体燃料,电力从煤经气化和氢气,二氧化碳捕获和存储。
包含在合成燃料生产。
这样一个系统的一个例子(侯赛因et al ., 2005)是一个600兆瓦的二甲醚(包含27%的煤炭输入能量和20%的煤碳)+ 365兆瓦的电力(H2)来自煤炭。对于这个系统二氧化碳存储率(相当于C煤炭的74%)是3.8 Mtonnes一年级从上游的合成反应器(39%)。估计燃料二甲醚cycle-wide温室气体排放是0.9倍的原油成油柴油和电力的0.09倍的43%高效燃煤电厂二氧化碳排放。
3.5.2.9变压吸附
变压吸附(PSA)是系统的净化合成气的首选,在高纯度氢气是必需的。然而,它并不选择性分离二氧化碳和其他废气所以鼻中隔黏膜下切除术后的应用程序废气中的二氧化碳浓度将40 - 50%,需要进一步升级到生产纯二氧化碳储存。同时H2和CO2分离是可能通过使用额外的PSA部分移除二氧化碳H2分离步骤前,如空气产品双子座流程(Sircar, 1979)。
PSA过程是建立在吸附分离的循环特征。周期包括两个基本步骤:吸附、中越能吸附的物种都是有选择地从原料气和再生(解吸),当这些物种从吸附剂中删除,这样就可以准备下一个周期。可以获得有用的产品在吸附和再生。PSA工艺的主要特点是使用减少压力和/或清除少能吸附的气体净化吸附床。除了吸附和再生,一个商业PSA周期包括许多额外的步骤,包括co和逆流增压、压力均衡,合作和逆流减压。详细描述的PSA技术,及其实际应用可以找到其他地方(鲁斯温et al ., 1994)。
的化学反应,可以通过减少压力和加热被逆转。叔胺methyldiethanolamine (MDEA,见下表3.2)广泛应用于现代工业过程中,由于高二氧化碳加载可能和低蓄热器热负荷,相对于其他溶剂。热碳酸钾(最常见的商业版本称为苯菲尔)用于二氧化碳去除氢在大多数植物大约15年前。
3.5.2.11物理溶剂过程
物理溶剂(或吸收)过程大多是适用于气体流的高二氧化碳分压和/或高总压强。他们常常被用于移除二氧化碳CO2和H2混合流的预燃室,来自于转变反应二氧化碳捕获流程,如产品的部分氧化煤和沉重的碳氢化合物。
主要物理溶剂过程如表3.2所示。溶剂的再生是由压力释放的二氧化碳从溶剂,在一个或多个阶段。如果需要更深入再生溶剂将被加热。流程ios版雷竞技下载 的能源消费,因为只有加压溶剂(液体泵)是必需的。
使用高硫bet雷竞技 在预燃捕获过程的结果在H2S的合成气。酸气组件必须被删除。如果运输和储存二氧化碳和硫化氢混合一起是可能的这两个组件可以被删除。Sulphinol开发达到溶解性明显高于酸性组件与胺溶剂相比,没有添加过度腐蚀的问题,降解发泡或解决方案。它由sulpholane的混合物(四氢噻吩1-dioxide),一个链烷醇胺和水在不同的比例根据职责。如果需要纯二氧化碳,然后选择性过程需要使用物理溶剂——通常Rectisol或Selexol。硫化氢必须分开在足够高的浓度(一般> 50%)治疗在硫回收设备。
3.5.2.10化学溶剂过程
化学溶剂用于把二氧化碳从合成气在局部压力低于1.5 MPa (Astarita et al ., 1983)和类似用于燃烧后捕集技术(见3.3.2.1节)。溶剂移除二氧化碳从移位的合成气
3.5.2.12对其他污染物的影响
预燃捕获包括改革,部分氧化气化。为了保持催化剂的可操作性的改革者,硫(H2S)改革之前被移除。在气化、合成气中硫可以捕获,并在液体或固体燃料气化时,微粒,NHj,因为和HCN系统中也存在需要移除。一般来说,所有的这些污染物可以从高压燃气燃烧之前,在燃烧产品稀释用氮气和氧气过剩。氢或hydrogen-containing燃料燃烧的气体,不可能形成的。根据燃烧技术和氢分数,氮氧化物的形成可能会有所不同。如果体积分数氢的低于约50 - 60%,氮氧化物的形成是在同一水平上对于天然气干燥低不系统(Todd和巴蒂斯塔,2001)。x
一般来说,除了可以co-removed H2S与CO2,其他污染物识别上面的额外预处理分离操作,尤其是在系统,液体或固体燃料气化。这些多元的污染,避免冷却高温预处理操作的合成气的优势提高整个气化过程的循环效率,但这些分离过程没有商业展示。
尽管尚不规范的标准污染物,水银(汞),目前相当关注的焦点作为污染物从煤炭电力系统。Hg气化系统可以恢复从合成气在环境温度非常低成本、Hg相比从烟道气体中复苏(·凯尔特et al ., 2002)。
3.5.3新兴技术
新兴的选择两个天然气和煤炭气化改革纳入小说结合反应/分离系统,如sorption-enhanced改革和sorption-enhanced水煤气转移,膜和膜水煤气改革转变。最后有一个范围的技术,利用碳酸化作用曹的二氧化碳捕获。
3.5.3.1吸附增强反应
一个概念称为吸附增强反应(SER)使用一个包含的混合催化剂填充床和选择性吸附剂去除二氧化碳从高温反应区,从而推动反应完成。(方式et al ., 1999)。定期再生吸附剂的使用压力,或与蒸汽温度吸附系统再生(方式et al ., 2005)。
高温二氧化碳吸附剂等水滑石(方式et al ., 1999)或硅酸锂(中川和大桥,1998)可以与催化剂促进混合蒸汽甲烷重整反应(反应1)或水煤气转移反应(反应3)生产纯氢和纯二氧化碳在单一加工单位。连续去除二氧化碳的吸附反应产物的变化对完成每一个反应。
SER可以用于生产氢气在400 - 600摄氏度燃料燃气轮机联合循环发电系统。设计研究基于通用电气(General Electric) 9 fa燃气轮机热氢,产生从空中吹ATR吸附增强水煤气转移反应堆,给理论净效率48.3%与90%的二氧化碳捕获99%的纯度和150条压力(方式et al ., 2005)。目前在试验工厂阶段过程。
3.5.3.2膜反应器制氢和二氧化碳捕获
无机膜与操作温度高达1000°C提供的可能性的氢的反应与分离相结合在高温和压力,克服单级平衡限制在传统的反应堆配置生产氢。分离和反应膜蒸汽转化和/或膜水煤气转移提供了更高的转换的改革和/或转移反应由于这些平衡反应的氢所示分别反应(1)和(3)。改革的反应是吸热的,可以用这个技术,被迫以较低的温度比正常完成(通常是500 - 600°C)。反应是放热的转变可以被迫完成在更高的温度下(500 - 600°C)。
把氢气分离膜的另一个原因产生的氢生产系统是,二氧化碳也是不需要额外的分离设备。膜反应器允许一步改革,或一个中间水煤气转移反应,与氢分离(渗透)留下一个滞留物气体,主要是二氧化碳和少量的non-recovered氢和蒸汽。二氧化碳维持在相对较高的压力反应系统(见图3.17)。凝结蒸汽的叶子集中在高压二氧化碳流,减少压缩能量传输和存储。膜改革将受益于高压操作由于H2部分跨膜压差增加氢渗透的驱动力。因此膜反应器、预燃室也被视为一个很好的选择de-carbonization在低压氢气流燃气和高压气体流运输和存储要求。膜的使用改革者反应堆在燃气轮机联合循环意味着产生的氢气需要在这种压力的重要的电力消耗氢压缩是可以避免的。这可以通过增加膜反应器的操作压力或通过使用尾气,例如蒸汽,在膜的渗透侧(Jordal et al ., 2003)。
对这些膜反应器的概念,一个氢选择性膜能够在高温操作,高压的环境是必要的。在文献中许多膜类型已报告有这些功能,这些都列在表3.3。基于表面微孔无机膜扩散分离展览,而低分离因素(例如,H2 / CO2分离系数的15)。然而,当前商用gamma-alumina的分离能力和硅微孔膜(有更好的分离因素,40)取决于稳定的膜孔隙大小,这是不利
-
- 图3.17膜反应器的工作原理。
微孔 |
微孔 |
微孔 |
沸石 |
金属 |
陶瓷 |
陶瓷 |
碳 |
继续阅读:地质储存是什么
这篇文章有用吗?